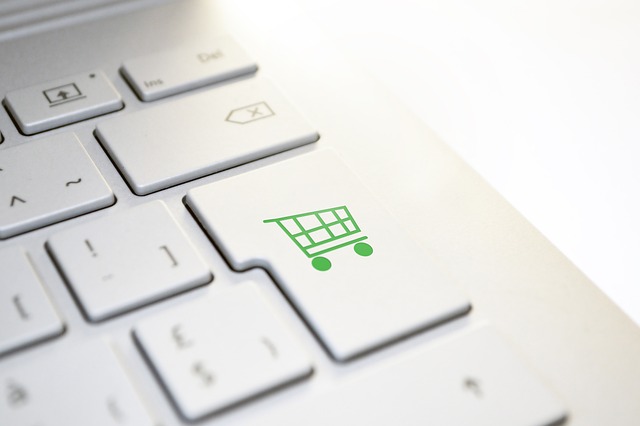
E-commerce, Ecology, and Continuous Improvement
Explore the economic impact of poor retail inventory management & a French law on unsold goods, with e-commerce’s ecological shift.
In the ever-evolving world of manufacturing, businesses are constantly seeking ways to meet their operational demands. While some adhere to traditional methods, relying on forecasts to produce goods in advance (make-to-stock), others adopt a more dynamic approach by crafting items based on specific customer orders, known as make-to-order (MTO).
For make-to-order businesses, efficiently managing materials for maintenance operations can be a complex challenge, given the minimal forecasting involved. In this article, we’ll delve into the unique challenges faced by MTO businesses when it comes to maintaining effective maintenance operations and explore how intelligent material management solutions can provide effective remedies.
Make-to-order (MTO) manufacturing stands apart from conventional production techniques. It entails creating products only after receiving customer orders, reducing the need for stockpiling finished goods but presenting a set of distinctive challenges.
Two critical aspects are ensuring the timely availability of maintenance parts and raw materials, two fundamental requirements to prevent disruptions in operations.
Operating in an environment with limited demand visibility and extended lead times, MTO businesses face unique hurdles. Since production is driven by specific customer orders, there’s minimal room for forecasting maintenance and material availability needs, resulting in uncertainty and challenges in ensuring the availability of critical maintenance parts and materials.
Which can lead to unplanned downtime, increased costs, and customer dissatisfaction. A disruption in maintenance operations due to the unavailability of essential parts and materials can have cascading effects on the entire manufacturing process.
Intelligent material management solutions, such as Flowlity, offer a ray of hope to MTO businesses grappling with maintenance material replenishment challenges.
These solutions harness technology and real-time data analytics to optimize material replenishment processes.
By continuously monitoring inventory levels, these solutions help businesses identify when maintenance parts are running low, enabling proactive replenishment. They also seamlessly integrate with supplier systems, facilitating real-time communication, reducing lead times, and ensuring the timely delivery of parts and materials.
The advantages of intelligent material management solutions in the context of MTO maintenance operations are significant. They empower businesses to:
In the realm of make-to-order manufacturing, maintaining efficient maintenance operations is paramount. While the challenges are indeed specific due to limited forecasting, it’s crucial to discuss the benefits of intelligent material management solutions.
These solutions, such as Flowlity, empower MTO businesses to optimize maintenance material replenishment, reduce downtime, minimize costs, and enhance supplier collaboration.
Explore the economic impact of poor retail inventory management & a French law on unsold goods, with e-commerce’s ecological shift.
What are the latest e-commerce trends and best practices in e-commerce? Jérémie Serout, Sales Manager at parcelLab is sharing tips and customer stories with us!
Explore how the e-commerce landscape has evolved, driven by increasing complexity, rising consumer expectations, and global competition.